- About AOSIBO
1.ASB High Temperature Tunnel Kiln for Faucet Ceramic Mixing Cartridges
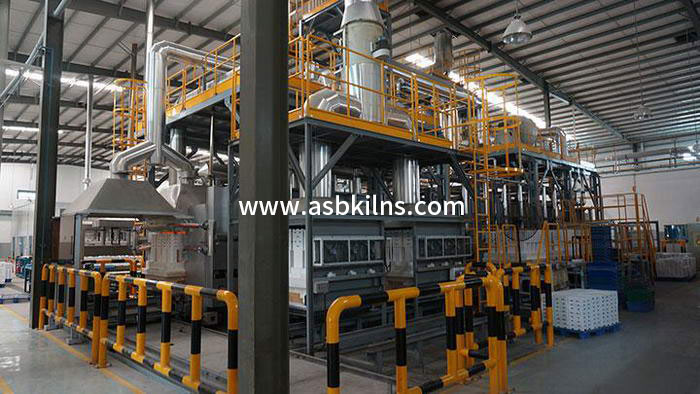
Ceramic cartridges are key part in faucets and other types of valves, which is one kind of special technical ceramic with a long service life, excellent sealing performance and no environmental pollution.
Traditionally use electric furnace as a mode of production, but which is big power consumption, small production, and take up production area and high maintenance cost. ASB designed a high temperature tunnel kiln for a well-known Spanish ceramic cartridges company produced in mainland China. The tunnel kiln firing with natural gas, which output is approximately equal to 4.3 times of the same length of electric kiln after production. The kiln is fully automatic operation, firing stability of low energy consumption, brought direct social benefit and economic benefit for the users. This design at the same time apply to an European factory of a well-known Hungary ceramic cartridges company .
The tunnel kiln has an effective length of 19.8 meters with a working temperature of up to 1,650°C. The Kiln is designed to have 15 cars inside the Kiln and 8 cars outside the Kiln in external cooling stations, Unloading and Loading areas and waiting area. The average daily output from the Kiln is 80,000 pieces (pure alumina ceramic mixing cartridges).
1.The ASB high temperature tunnel kiln is constructed to proven European designs, with British engineers involved in the engineering requirement, installation and final commissioning. The Kiln structural design, Combustion systems and Electrical controls incorporate the requirements of European standards including (EN746-2, EN 60204-1).
2.The Kiln offers safe and stable operation with proven structural design, advanced combustion control technology and precise temperature control and monitoring. Temperature differentials and Energy consumption are low. The kiln Haulage system is equipped with fully automatic transfer vehicles and kiln car automatic return rail haulage system.
3.The Kiln control system includes data recording and state simulation, can be remote monitoring of kiln data, for plant engineers is available, including run time and production data, real-time view of kiln tunnel, kiln head, and exhaust system.
4.For the kiln entrance exhaust system equipped with afterburner for the effective incineration of binder products from the exhaust gases, meeting future environmental protection requirements.
5.Waste heat recovery system: Kiln waste heat from the cooling section is used to pre-heat the burner combustion air and kiln entry pre-heating.
ASB can supply multi-type, cost-effective high temperature kiln according to customer's specific requirement.
2.New Bogie Hearth Electrically Heated Furnace 2016
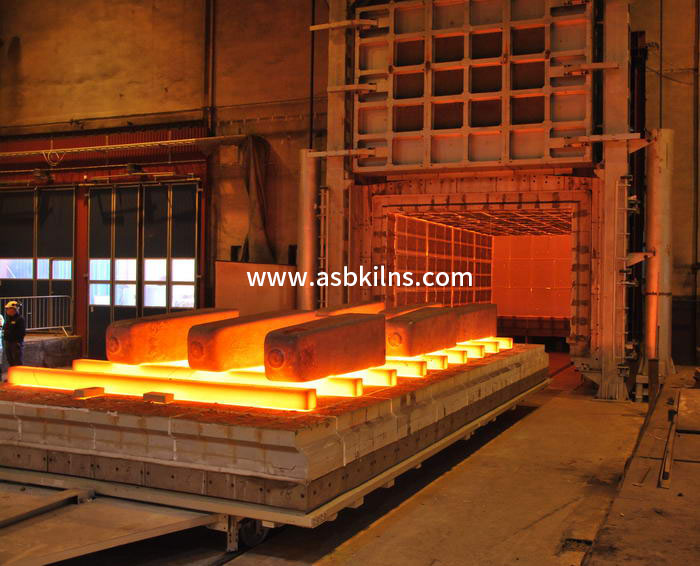
This new Bogie hearth furnace with Guillotine Door has been installed in Sweden at the works of an Internationally recognised Swedish Company.
With a load capacity of 24,000 kg including supports, the furnace heats multiple Special Steel Ingots to a maximum temperature of 1,250˚C.
Heating is provided by Kanthal APM material installed as corrugated rod elements in 4 Temperature Control Zones distributed in the sidewalls and roof of the furnace. The total thermal input is 550 kW, with a minimum heating rate of 60˚C/hour.
During normal operation, the furnace door is opened and the bogie car driven out to allow individual Ingots to be picked from the bogie and taken to the Rolling mill.
Customer specific design requirements for a Door opening speed of 12 m/minute and a maximum Bogie speed (Fully out) of 30 seconds are incorporated into the mechanical design.
Door and Bogie Motor Drives are switched via VSD’s.
Power to the Furnace Elements is controlled via 4 PLC based PID controllers, Thyristors and Stepdown transformers.
All operating parameters and temperature data are logged via the PLC and can be accessed remotely via the customers existing LAN.
Selected Data including all operating parameters are also displayed on a locally mounted HMI.
ASB KILNS can supply multi-type, cost-effective Furnaces according to customer's specific requirements, including heating by Electricity, Gaseous Fuels and Oil.
3.New 42 metre long Tunnel Kiln 2016
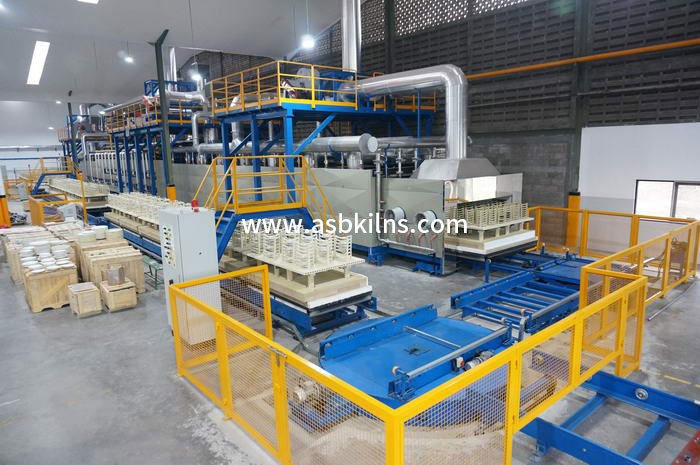
This new Tunnel Kiln has been installed in Indonesia and fires Fine China Tableware in open flame (No Saggers) conditions.
The tunnel kiln has an effective length of 44 metres with a working temperature of up to 1,250°C. The unit is designed to have 35 cars inside the Kiln and 23 cars outside, positioned in the Unloading/ Loading and waiting areas. Usable volume per car is 0.96 m³, with a designed daily output of 32,400 pieces (based on a 6 hour Cold - to - Cold firing cycle).
The ASB tunnel kiln is constructed to proven European designs, with British engineers involved in the engineering requirement, installation and final commissioning. The Kiln structural design, Combustion systems and Electrical controls incorporate the requirements of European standards including (EN746-2, EN 60204-1).
The Kiln offers safe and stable operation with proven structural design, advanced combustion control technology and precise temperature control and monitoring. Temperature differentials and Energy consumption are low. The kiln Haulage system is equipped with fully automatic transfer vehicles and kiln car automatic return rail haulage system.
The Kiln control system includes data recording and operating status. Remote monitoring of kiln data (Temperature, Status etc.), for plant engineers is available, including run time and production data, real-time view of kiln tunnel, kiln head, and exhaust system.
Waste heat recovery system: Kiln waste heat from the cooling section is used to pre-heat the burner combustion air and kiln entry pre-heating.
ASB KILNS can supply multi-type, cost-effective kilns according to customer's specific requirements.
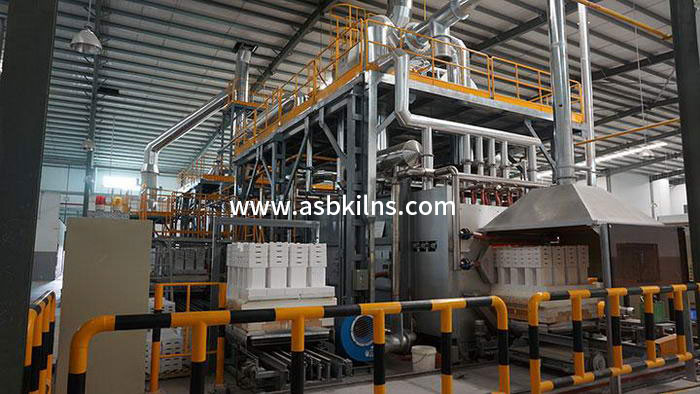
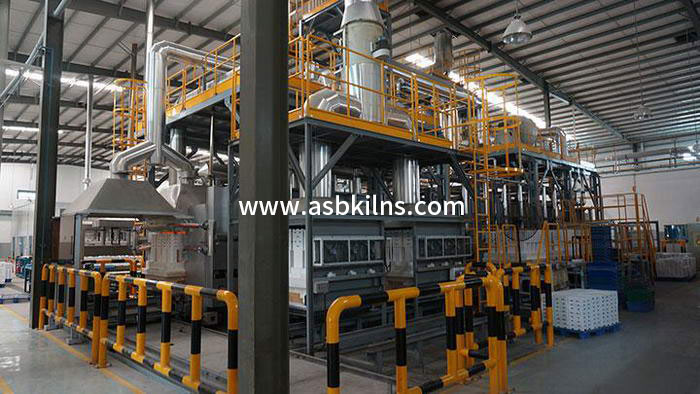
Ceramic cartridges are key part in faucets and other types of valves, which is one kind of special technical ceramic with a long service life, excellent sealing performance and no environmental pollution.
Traditionally use electric furnace as a mode of production, but which is big power consumption, small production, and take up production area and high maintenance cost. ASB designed a high temperature tunnel kiln for a well-known Spanish ceramic cartridges company produced in mainland China. The tunnel kiln firing with natural gas, which output is approximately equal to 4.3 times of the same length of electric kiln after production. The kiln is fully automatic operation, firing stability of low energy consumption, brought direct social benefit and economic benefit for the users. This design at the same time apply to an European factory of a well-known Hungary ceramic cartridges company .
The tunnel kiln has an effective length of 19.8 meters with a working temperature of up to 1,650°C. The Kiln is designed to have 15 cars inside the Kiln and 8 cars outside the Kiln in external cooling stations, Unloading and Loading areas and waiting area. The average daily output from the Kiln is 80,000 pieces (pure alumina ceramic mixing cartridges).
1.The ASB high temperature tunnel kiln is constructed to proven European designs, with British engineers involved in the engineering requirement, installation and final commissioning. The Kiln structural design, Combustion systems and Electrical controls incorporate the requirements of European standards including (EN746-2, EN 60204-1).
2.The Kiln offers safe and stable operation with proven structural design, advanced combustion control technology and precise temperature control and monitoring. Temperature differentials and Energy consumption are low. The kiln Haulage system is equipped with fully automatic transfer vehicles and kiln car automatic return rail haulage system.
3.The Kiln control system includes data recording and state simulation, can be remote monitoring of kiln data, for plant engineers is available, including run time and production data, real-time view of kiln tunnel, kiln head, and exhaust system.
4.For the kiln entrance exhaust system equipped with afterburner for the effective incineration of binder products from the exhaust gases, meeting future environmental protection requirements.
5.Waste heat recovery system: Kiln waste heat from the cooling section is used to pre-heat the burner combustion air and kiln entry pre-heating.
ASB can supply multi-type, cost-effective high temperature kiln according to customer's specific requirement.
2.New Bogie Hearth Electrically Heated Furnace 2016
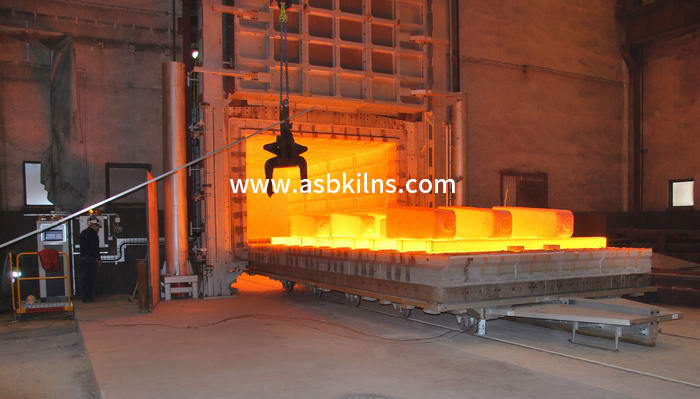
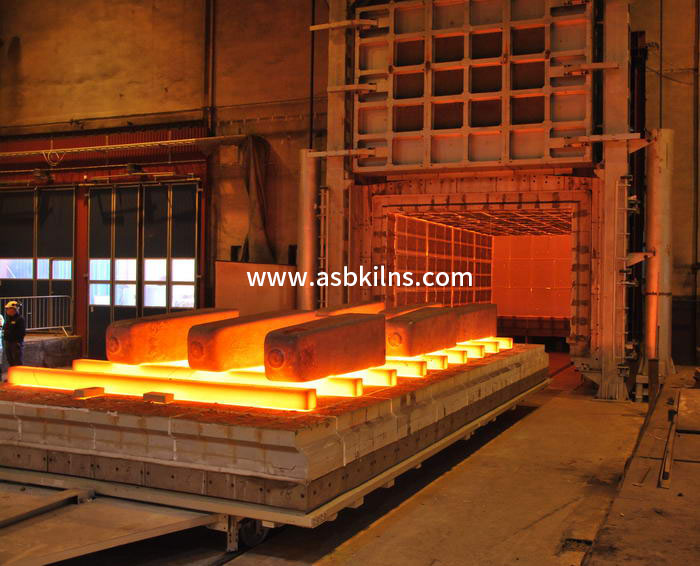
This new Bogie hearth furnace with Guillotine Door has been installed in Sweden at the works of an Internationally recognised Swedish Company.
With a load capacity of 24,000 kg including supports, the furnace heats multiple Special Steel Ingots to a maximum temperature of 1,250˚C.
Heating is provided by Kanthal APM material installed as corrugated rod elements in 4 Temperature Control Zones distributed in the sidewalls and roof of the furnace. The total thermal input is 550 kW, with a minimum heating rate of 60˚C/hour.
During normal operation, the furnace door is opened and the bogie car driven out to allow individual Ingots to be picked from the bogie and taken to the Rolling mill.
Customer specific design requirements for a Door opening speed of 12 m/minute and a maximum Bogie speed (Fully out) of 30 seconds are incorporated into the mechanical design.
Door and Bogie Motor Drives are switched via VSD’s.
Power to the Furnace Elements is controlled via 4 PLC based PID controllers, Thyristors and Stepdown transformers.
All operating parameters and temperature data are logged via the PLC and can be accessed remotely via the customers existing LAN.
Selected Data including all operating parameters are also displayed on a locally mounted HMI.
ASB KILNS can supply multi-type, cost-effective Furnaces according to customer's specific requirements, including heating by Electricity, Gaseous Fuels and Oil.
3.New 42 metre long Tunnel Kiln 2016
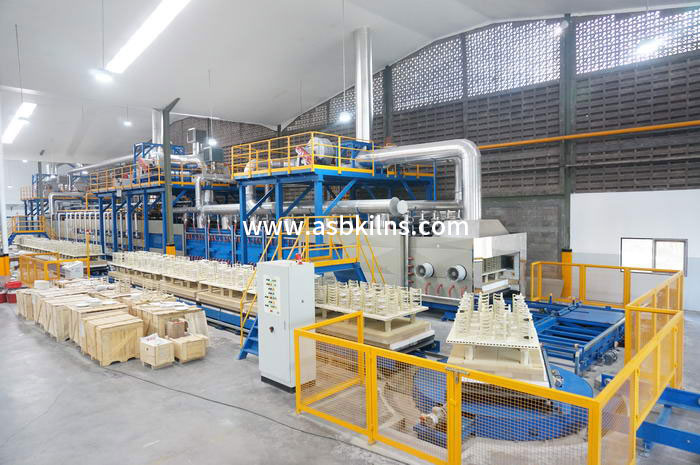
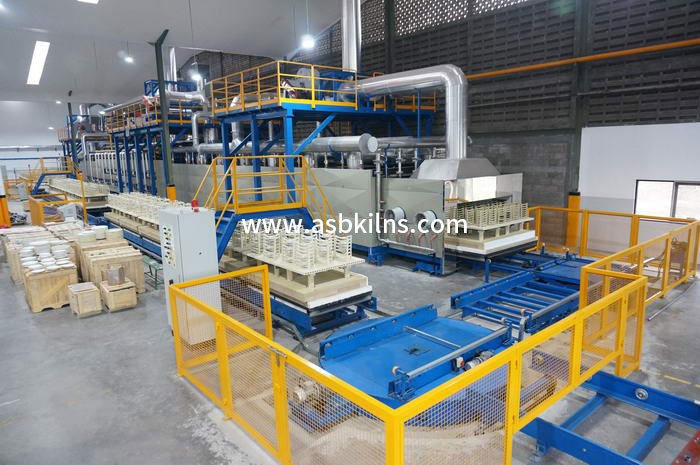
This new Tunnel Kiln has been installed in Indonesia and fires Fine China Tableware in open flame (No Saggers) conditions.
The tunnel kiln has an effective length of 44 metres with a working temperature of up to 1,250°C. The unit is designed to have 35 cars inside the Kiln and 23 cars outside, positioned in the Unloading/ Loading and waiting areas. Usable volume per car is 0.96 m³, with a designed daily output of 32,400 pieces (based on a 6 hour Cold - to - Cold firing cycle).
The ASB tunnel kiln is constructed to proven European designs, with British engineers involved in the engineering requirement, installation and final commissioning. The Kiln structural design, Combustion systems and Electrical controls incorporate the requirements of European standards including (EN746-2, EN 60204-1).
The Kiln offers safe and stable operation with proven structural design, advanced combustion control technology and precise temperature control and monitoring. Temperature differentials and Energy consumption are low. The kiln Haulage system is equipped with fully automatic transfer vehicles and kiln car automatic return rail haulage system.
The Kiln control system includes data recording and operating status. Remote monitoring of kiln data (Temperature, Status etc.), for plant engineers is available, including run time and production data, real-time view of kiln tunnel, kiln head, and exhaust system.
Waste heat recovery system: Kiln waste heat from the cooling section is used to pre-heat the burner combustion air and kiln entry pre-heating.
ASB KILNS can supply multi-type, cost-effective kilns according to customer's specific requirements.